該網站可用中文
(This webpage is available in mandarin.)
(This webpage is available in mandarin.)
German Quality Control Expert in Power Supply Industry
The main services of Steel Inspect include:
- Planning, monitoring and supporting of projects worldwide in the field of construction of power systems, engineering systems, industrial plants and wind offshore farms
- Using a top-skilled interdisciplinary team
- We ensure high-quality and on-time completion based on Q7 Approach
- Reliable partner for companies faced with the inevitable challenges involved in complex execution projects
- All quality inspections are carried out in compliance with the respective applicable standards and guidelines related to the project
- Steel Inspect supports a project either during a specified phase or throughout all stages, from the design and initial procurement until it‘s handed over to the client.
Facts and Figures
- Yearly turnover > € 3 million
- 20 high qualified fully employed quality management specialized staff
- 20 fix freelancers, hiqhly-qualified quality management specialists, who work for Steel Inspect on permanent basis
- Candidate pool of worldwide 5,000+ pre-qualified quality management specialists
Main Value of Our Service
Efficiently Reduce Costs of Quality.
Improve Time Awareness.
More Values of Our Service
Philosophy
Quick and proper response to all technical challenges based on history, experience response, qualification and practical approach.Quality
Comprehensive quality control at all execution stages – at suppliers and construction sites.Fabrication
Efficient monitoring of fabrication status, supplier quality, product traceability, timeline, construction conditions, quality and progress.Expediting
Point out and continuous follow up of potential risks from quality and delivery schedule at an early stage.Mindset
Not acting as problem-documenter or administrator, but rather as problem solver and active fabrication consultant.Costs
Optimization of manpower, inspection and monitoring time / use of supplier synergies and avoiding of idle times.The 7 Phases of Quality Control
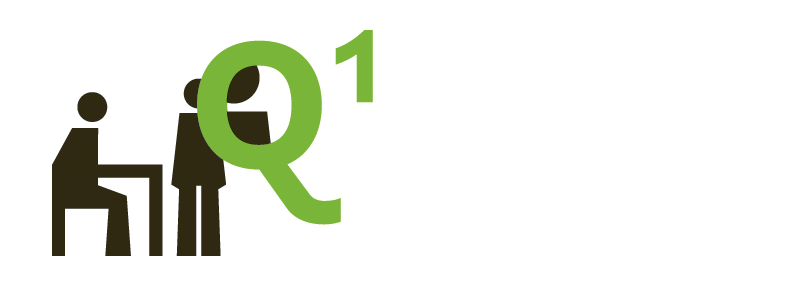
Design Check and Procurement
- Advanced risk assessment in terms of manufacturing design and construction experience based on former projects
- Evaluation of design, product and process FMEA’s
- Evaluation of feasibility studies / Employer Requirements
- Consulting cost-effective design and specification optimization / design check
- Consulting selection process for suitable suppliers / OEM/Contractor/Supplier Assessments / OEM Integration Concept
- Execution and evaluation of supplier and process audits (VDA 6.3)
- Project Quality Control Plan / Master Document List (MDL)
- Document Delivery Schedule (DDS)
- Verify supplier certificates and quality documentation / FabrPreview
- Execution of kick-off meetings / planning of milestones / inspection schedule milestones / inspection plans
- Recruitment of intercultural monitoring teams
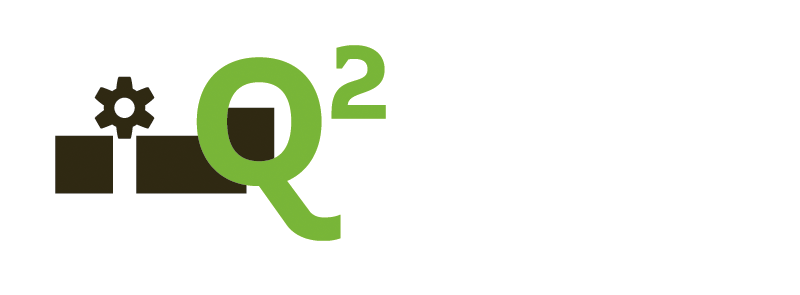
Manufacturing Control and Expediting
- Manufacturing monitoring on permanent or on regular basis
- Process consulting and continuous quality improvement
- Focus on Welding, NDT, Coating and Documentation Control / Review
- Status inspections as required as well as per ITP
- Coordination and support of suppliers / assessment of sub-contractors
- Expediting / Status reporting with traffic light for Quality, Delivery, Costs
- Creation, administration and tracking of NCR’s
- CIP during manufacturing / lead of punch lists
- Preparation and execution of claim management
- Regular plausibility check of delivery schedule versus production
- Analysis Critical Path in production, analysis of available and necessary resources
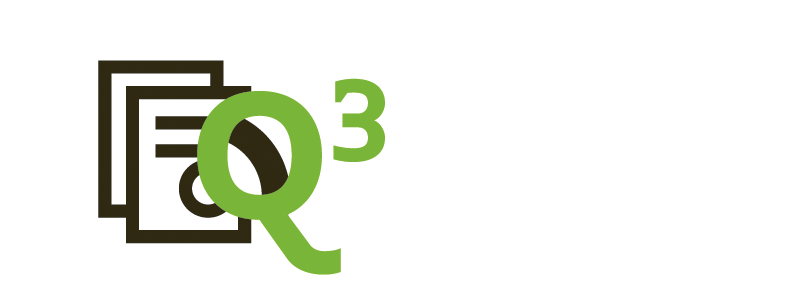
Documentation Process
- Documentation check according specifications, customer-, 3rd parties- and authorities requirements
- Kick Off Meeting Document Preparation
- Guidance and support of the supplier during the documentation preparation / Workshop Documentation Structure
- Creation of deviation list for each documentation individually
- Status reporting Documentation with traffic light for Quality, Delivery, Costs
- Creation of individual requirement profiles for the content and form of the documentation
- CIP during check of documentation / completeness check
- Administration and tracking of NCR’s and punch lists
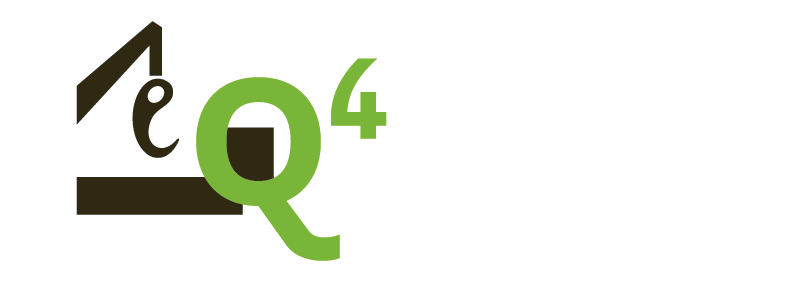
Inspections prior to Transport
- Preparation and editing of the hand over documentation
- Carrying out final inspections and pre-shipment inspections
- Supplier FAT Control
- Carry out completeness checks according to customer requirements
- Preparation and documentation for claim management
- NCR creation, management and tracking
- Creating, managing and tracking LoP lists
- Supplier Transmittal & Change Control
- Supplier delivery Coding & Labelling
- Shipments, Crades, Packing Lists
- Tagging ID, Bar Codes, RFIDs
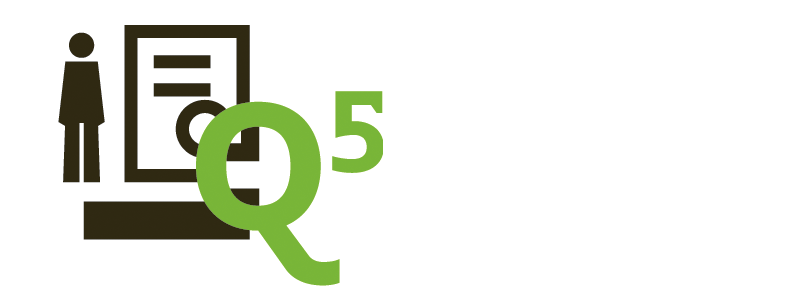
Preparation for Erection & Installation
- Completeness checks and incoming inspections / on time component providing
- Prepare of inspection checklists / defect and damage reporting
- NCR clearing and database set up
- Supervision of all pre-assembly activities in terms of Quality, Schedule and Costs
- Execution of pre-inspections and internal handovers / preparation of acceptance certificates
- Implementation of QC System according Employer Requirements, Codes and Standards
- Review of erection and quality documentation acc defined codes and requirements
- Implementation of permit to work system / HSE concept and training execution
- Set up of necessary manpower / Kick Off Meetings for HSE and Offshore Installation Planning
- Preparation of QC checklists and NCR system
- Establishment of communication and reporting system
- Review of quality assurance documents like method statements, execution plans, risk assessments etc.
- On-time component providing / timely loading / shift and assignments schedules
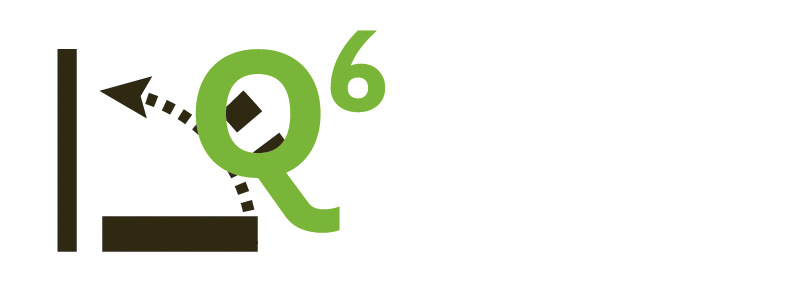
Erection and Commissioning Stage
- Complete HSE, QC and construction supervision during offshore installation / conducting QC
- Coordination of HSE and QC manpower
- Setting up relevant reporting and distribution system for daily communication
- Execution and leading of Kick Off and daily site meetings
- Status reporting with traffic light for Quality, Delivery and Costs
- Continuous plausibility check of progress and schedule
- Analyses of critical installation issues and available versus necessary resources
- Update and follow up of ITPs / Inspection execution with clients and 3rd Parties
- Ensuring of contractually agreed quality participation and witnessing
- Document system for claim management, punch lists, NCR and checklists
- Maintain the documentation from start of construction to completion of installation
- Check and updating of assignment and crew schedules
- Tracking and recording of bad weather and technical down times
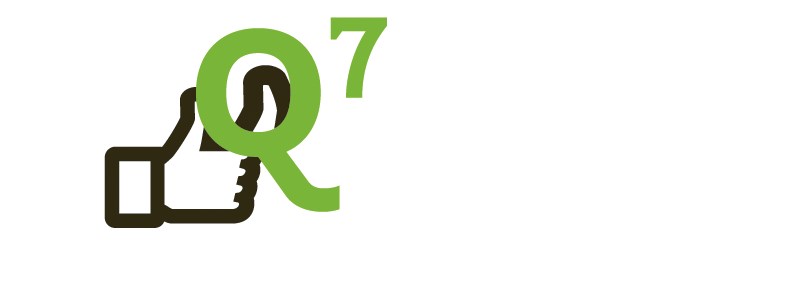
Final Acceptance and Handover
- Execution of final inspections with clients and 3rd Parties
- Completeness checks according client requirements
- Witnessing and documentation of final commissioning activities
- Ensuring and verification of final protocols and release documents
- Update, check and verification of NCR status and punch lists
- Final claim management list / verify status
- Final check, verification and structuring of erection and commissioning documentation according defined guidelines and employer requirements
- Preparation for handover to Client
- Evaluation of improvement potential and lessons learnt / installation of an Experience Response System